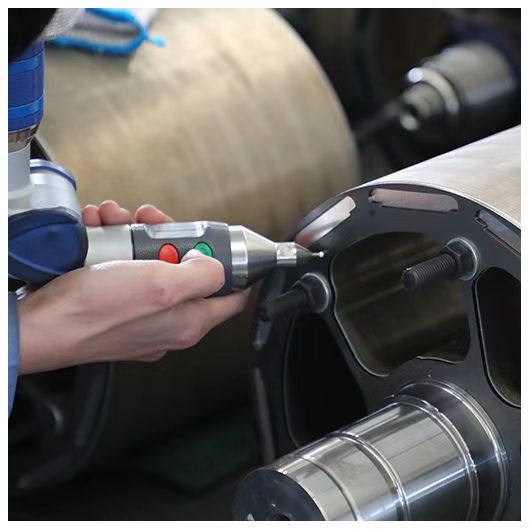
QUALITY CONTROL
In the field of industrial manufacturing, the accuracy of parts directly determines the performance of the product, and the stamping industry`s requirements for product accuracy have reached the micron level, which means that it is almost impossible to find defects in product quality with the naked eye. As an ISO 9001:2015 Certified company, Yongrong Power always provides qualified products to our customers, We have strict quality control procedures in every production process.
MATERIAL TRACK
Since the raw materials enter our warehouse, we will use professional instruments to test the physical and electromagnetic properties of each roll of silicon steel and record all the original information.
The raw material silicon steel coil will be cut according to the product size and rolled into a coil again. We will make an exclusive mark and a bar code on each roll of silicon steel coil, and this mark will appear on each subsequent process until it enters the customer's production workshop. The final result is that we can clearly know which steel mill produces the silicon steel used in the iron core of each motor and who are involved in the production process.
QUALITY ASSURANCE
Motor Lamination
We will strictly inspect all the dimensions of the first lamination with an image measuring instrument when the press start or when the new die is installed. In the production process, operators check the consistency of the laminations every 200 pieces of production. In addition, during the production process, quality inspectors randomly select laminations and inspect all sizes.
Motor Core
The inspection of stator core mainly includes appearance inspection, slot inspection and size inspection.
For the medium-large size cast aluminum rotor, We use X-ray system to inspect the porosity of the end ring. The inspection process and results will be recorded as videos and pictures and attached to the product inspection report.